ABB calls for better preparation during “lighthouse phase”
ABB Consulting recommends that operators should make better preparations during the "lighthouse phase" to avoid cost increases when the time comes for full scale decommissioning.
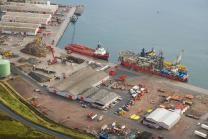
The squeeze on operating margins caused by the continuing slump in oil prices is prompting many firms to delay the full-scale decommissioning of their offshore assets resulting in an extension of the “lighthouse phase”.
Brian Twomey, the managing director of Reverse Engineering, told Decom World that firms should be aware that many platforms that have been in service for several decades require increased spending on maintenance in the run up to disposal.
Operators are failing to plan for this, and as a result are dramatically increasing the costs they will pay when they eventually come to dispose of the asset. Altogether, about 500 offshore installations will be decommissioned over the next seven years, at a cost of £10.4bn. Besides Brent, CNR International’s Murchison field is currently being dismantled, and Marathon Oil’s Brae field will shortly follow.
Twomey said: “Many platforms are getting to the point that if you don’t maintain them after they finish producing, you move from decommissioning towards salvage, and that’s a place you don’t want to be. There are many more unknowns, and the salvage cost could be 12 times the decommissioning cost.”
Piece small decommissioning
ABB Consulting has recently carried out a survey and a number of workshops with operators and service companies to discuss the strategies and issues that arise when decommissioning is carried out in stages with an extended lighthouse period.
Dai Richards, Global Marketing Manager with ABB Consulting, said some problems had arisen because firms had not thought through their approach to “piece small” decommissioning.
He said: “There have been a number of examples where companies have got rid of elements, or have stopped maintaining elements that they later found they needed. They think: I don’t need any accommodation or I don’t need cranes or navigations systems and then they realise later, yes I do.”
“Part of our message to people is that you really can save yourself a lot of money down the line by spending a little bit upfront to maintain the kit that needs to be maintained. So you still need to preserve the equipment that you need to complete the work, and that can be quite expensive,” he added.
There is a tendency among some firms to take a zero cost option by simply “switching it off and walking away”.
“That might be an attractive option this year or next year for your budget but the guy who picks up the problem when you do have to decommission will not thank you. We’ve certainly seen examples of people who are not thinking it through as well as they could do,” Richards explained.
The importance of this issue has been increased by indications that companies are bringing forward their decommissioning plans. For example, the largest programme of works will be Shell’s 10-year plan to decommission its Brent field, and the company asked DECC for permission to begin this at the earliest possible date.
Life support systems
One possibility for operating platforms during the lighthouse period is to replace the existing power and automation systems with a package designed to provide the minimal functions needed to keep the elements that will be required for decommissioning in working order.
ABB Consulting is developing a modular power unit that can be craned onto platforms for that purpose, but as yet none have been deployed.
Richards explains that this system can help to segregate work, creating fewer issues, when it comes to dismantling a platform for lift or cutting. This is a difficult undertaking when the work is being done around all the embedded navigation systems.
“What’s needed is a cost-effective, easy-to-implement solution that gives you all the life-support type systems that you need to continue to operate when you’re not producing your own power and it also gives you a clear path,” Richards said.
Redundant systems
According to Richards, piece small decommissioning of some elements can begin while the asset is still in operation, but many firms fail to carry it out.
“The partial decommissioning of assets brings various benefits that most operators can avail themselves of now. Most people will have some redundant equipment or systems that is adding weight to the platform and takes up space,” Richards said.
“There are cases where a whole production platform has been tied back into another platform and it’s just being used for export – then most of its topside processing equipment is redundant,” Richards added.
According to Richards, operators are often reluctant to sell on their second-hand machinery, and also fail to retire it properly.
“If it doesn’t immediately help production it tends to be ignored, and in many cases it isn’t isolated from alarm systems. When it comes to doing that work there’s a time issue and a process issue so it might be less hassle for some firms to get someone in who has a slick methodology for getting it done efficiently.”
A report for the Performance Forum in 2013 found that the average time that facilities were in lighthouse mode before the advent of cheap oil was more than three years, however even without issues of cost deferral and capacity constraints this is likely to be longer in the case of the larger facilities in the northern quadrant of the North Sea. BP’s Miller platform, for example, ceased production in 2009 and has been a “minimally manned installation” since then, as well as a base for the Jigsaw search and rescue helicopters.